


Engineering Analysis
Using a typical fascia design, an engineering study was conducted using AutoDesk Mold Flow analysis software. The goal was to produce a mold using conventional cooling methods and another using the patented Conformal Cooling Solutions process
Important criteria to analyze included;
-
Time required before part ejection
-
Surface temperature
-
Part warpage or distortion
-
Molding cycle time
-
Coolant circuit pressure and in-out temperature delta

Conventional cooled gundrilled core holes 100 drilled holes, baffles and bublers

Conventional cooled core showing part surface temperature. Note hot spot area

Conventional cooled core showing circuit temperatures. Note the higher in and out temperature deltas

Conventional cooled core showing circuit pressure through the system

Conventional cooled core part deflection in the Z plane (warpage)

Conventional cooled core showing ejection readiness after 15 seconds. Note amount of hot spots thus requiring additional cooling time
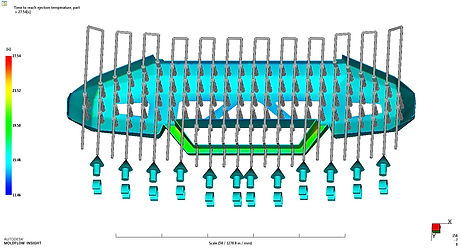
Conventional cooled core showing ejection readiness after 27.5 seconds. Note remaining hot spot thus requiring additional cooling time

Conformal cooled CCS channels
Note available space for slides, pins and lifters

Conformal cooled core part temperature showing much more cooler areas

Conformal cooled core showing circuit temperatures. Note the much smaller in and out deltas

Conformal cooled core showing circuit pressure through the channels. Note design reduces pressure by 20X

Conformal cooled core showing part deflection in the Z plane. CCS system reduced warpage by 60%

Conformal cooled core showing ejection readiness after 15 seconds. Additional MoldFlow analysis would be required to eliminate or reduce the remaining hot spots

Conformal cooled core showing ejection readiness after 27.5 seconds. CCS system reduced this time by 3.42 seconds but additional MoldFlow analysis would have allowed further decreases in time. Past test run on production tool showed a decrease of 25% versus conventional cooling